The Nitty Gritty
- What is a work order?
- How do you know which type of work order to use for your business?
- What essential things must you always include in your work orders?
- What effective steps can you follow in order to create efficient work orders?
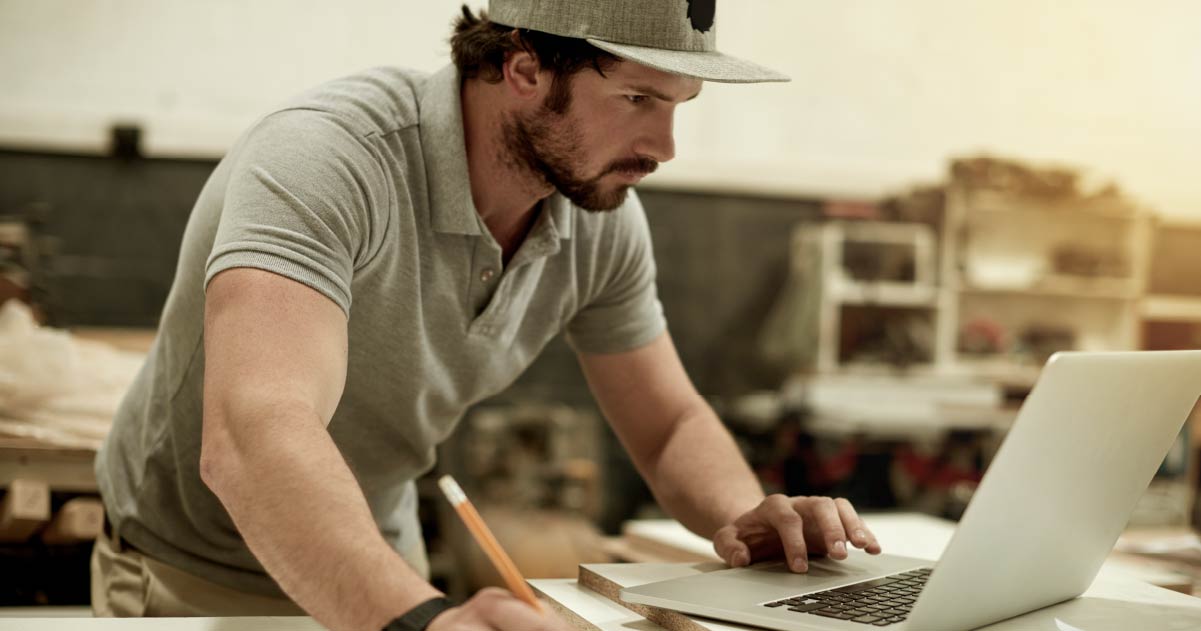
Creating effective work orders is key to ensuring your business runs smoothly and efficiently, and helps toward keeping your customers well informed regarding the work being carried out. Before you can maintain this workflow, it’s important to get to grips with a work order process, understand how to organize work orders and most importantly, to understand: What is a work order?
What Is a Work Order?
A work order is a detailed description of any preventative or corrective maintenance work that a business is carrying out. There are a couple of other types of work order which we’ll dive into a little later on in the blog. A work order ensures that everyone involved is aware of their responsibilities and expectations in regards to the job or project.
Work orders are widely used across the field service industry including plumbing, construction, fire safety and HVAC maintenance and installation. There are many benefits in having a work order process, one of them being the ease of tracking labor and materials used in the completion of a job. By having this detailed record associated with each job, you can ensure they stay within budget. Additionally, tracking progress with work orders allows you to ensure jobs are completed on time, and are able to give your customers an accurate estimate of a completion date. That also leaves you with a bunch of happy customers.
Different Types of Work Orders
There are several different types of work orders that can be used depending on the needs of a particular job or project. A work order in construction projects may differ from what is needed for a maintenance work order. In other words, not every type will be applicable depending on the business. Let’s take a look at a few examples of some of the most common types of work order.
General work order. This involves work that doesn’t fall under some form of maintenance request; preventative or corrective. For example it may be setting up new equipment, dismantling new equipment, painting and all sorts of other smaller jobs.
Corrective work order. This revolves around maintaining systems, equipment or machinery that is already set up. Sometimes specialized equipment and tools may be required, or perhaps maintenance staff with a specific skillset. There may also be occasions where corrective work is required at the same time as a preventative maintenance visit. The purpose of corrective maintenance is to restore the functionality of the equipment, machinery or systems so it can be restored to the correct condition.
Preventative work order. This type of work order is scheduled in advance, routine maintenance tasks that are required within a specific time-frame. It’s usually work that needs to be completed in order for the equipment to function as intended, to prevent further costs to the business and other unexpected malfunctions.
Emergency work order. There are always going to be times when equipment, machinery and systems go down unexpectedly. And it’s times like these where an emergency work order is required. It’s reactive maintenance so extremely important you gather all the correct information and send out the right maintenance team for the job, as it could be time-critical.
“In coming to understand how to organize work orders within your business and follow a work order process, you may need to go through a little trial and error.”
10 Things You Need to Include in Your Work Orders
As well as coming up with a solid work order management process, you need to make sure your work orders contain all of the relevant information for your customers. This includes things such as a description of the task, service requirements, completion date, materials required and much more. Let’s take a deeper look into what information makes for an effective work order.
Task and service requirements
Detail what asset requires maintenance work and the service required, depending on what type of work order you’re creating.
Resources and materials needed
There may be specific skill sets required for the work, which you can detail here. As well as the materials that may be required. This ensures you assign the right person to the job and they have everything they need on the day.
Overview of the issue
Make sure you have a description of the issue at hand, this way there can be no confusion for the customer about what’s expected from the work.
Date requested
This will be the date the customer initially made the enquiry or booked in the work. This shows your business is organized, and starts a timeline for the work to be completed.
Expected completion date
Forecast when you expect the work to be completed, it’s always tentative as there may be unexpected delays. Such as material shortages, weather delays or site closures.
Actual completion date
Here you can outline when the work was completed, even if it’s the same date as the expected timeframe. This type of detail also helps with forecasting similar work in the future.
Checklist of tasks
This helps maintenance technicians and other employees know what is expected to complete the task as well as giving the customer a clear understanding of the process. The tasks can be marked off as they’re completed.
Health and safety protocols
Different jobs require different health and safety legislation. It’s important to detail these terms so your employees can keep themselves and others safe.
Business details
Ensure you list your contact details as well as business address. This gives your customer an opportunity to reach out if they have any questions about the work during its progress or after completion.
Sign off area
An area for both customer and employee to sign. This is essentially a written agreement that all parties are happy with the work completed.
How to Create Effective Work Orders Step-By-Step
In coming to understand how to organize work orders within your business and follow a work order process, you may need to go through a little trial and error. However, there are a few field service management best practices that help towards building effective work orders. Let’s take a look at each one, step-by-step.
1. Identify the scope of the project
The first step in creating an effective work order is to determine the scope of the project. This includes outlining specific tasks that need to be completed, what materials, labor, and services are needed, and any relevant instructions or safety concerns. It's important to make sure that everyone involved understands exactly what needs to be done in order for the job to be completed.
2. Assign due dates
Once you have identified the scope of the project, it's time to assign due dates for each task. These due dates should account for any unforeseen issues that may arise during the course of completing a job, within reason. As there’s always the risk of an unexpected delay that’s impossible to see ahead of time. Additionally, assigning due dates helps ensure that all parties are working towards completing the work or project in an efficient manner. And it shows your customers that you run a well-oiled, tight ship.
3. Specify the labor and materials required
After you've identified what needs to be done and set due dates for each task, it's important to specify which materials, labor or services will be required for each job. This ensures that everyone involved knows exactly what supplies need to be purchased or rented before beginning a job so they can plan accordingly and budget properly. It also allows businesses owners to accurately track their costs associated with each job.
4. Include relevant safety instructions
It's important to not only include details about tasks needing completion but also any relevant instructions or safety concerns associated with those tasks. Such as personal protective equipment (PPE) requirements or hazardous chemicals being used onsite. This helps protect your employees from potential harm while ensuring compliance with regulations related to safety standards in the industry.
5. Establish a payment timeline
Lastly, you need to establish a clear payment timeline for the completion of any work. This way, both you and your contractors or employees know when payments will be made upon completion of a job. This helps avoid confusion further down the line with customers as well.
Bonus Work Order Template
What is work order management software? It is typically and end-to-end field service software that allows you to easily create and manage work orders. But if you don’t have access to a work order management software, here are some free work order templates to get you started.
Summary
Creating effective and efficient work orders is a process, one we hope has been made easier with this step-by-step guide. You know the answer to the question: What is a work order? And we’ve talked about work order management best practices, as well as what to include within your work orders.
If you’re looking for further information on how to keep your customers coming back to your business, check out our Customer Retention Strategies for Small Business blog.